
【编者按】
我们向万能的DeepSeek提出一些简单的半导体相关问题,看其回答能否满足你的要求。
问题:CVD、PVD和ALD三种薄膜沉积技术的对比分析
以下是
CVD(化学气相沉积)、PVD(物理气相沉积)和ALD(原子层沉积)三种薄膜沉积技术的综合对比,从原理、工艺特性、应用场景到市场趋势进行系统分析:1. 基本原理与工艺过程
PVD(物理气相沉积)
原理:在真空环境中通过物理方法(蒸发、溅射)使固体材料气化,气态粒子沉积到基片表面形成薄膜。
工艺过程:材料气化
→粒子传输→基片表面沉积(成核生长)。特点:沉积方向性强,存在视线效应(
line-of-sight deposition),导致复杂结构覆盖不均。CVD(化学气相沉积)
原理:气态前驱体在基片表面发生化学反应(热分解、合成反应),生成固态沉积物。
工艺过程:气体扩散→表面吸附→化学反应→副产物脱附。
变体技术:
LPCVD(低压CVD):低压环境提升均匀性,高温(600–850℃)。
PECVD(等离子增强CVD):等离子体辅助降低沉积温度(<400℃)。
MOCVD(金属有机CVD):用于化合物半导体(如氮化镓)。
ALD(原子层沉积)
原理:两种前驱体交替通入反应室,通过表面自限性饱和化学反应逐层沉积原子级薄膜。
工艺过程:前驱体
A脉冲→惰性气体冲洗→前驱体B脉冲→二次冲洗(循环进行)。特点:非连续沉积,每循环沉积一层原子(约
0.1nm),实现原子级厚度控制。2. 关键工艺特性对比
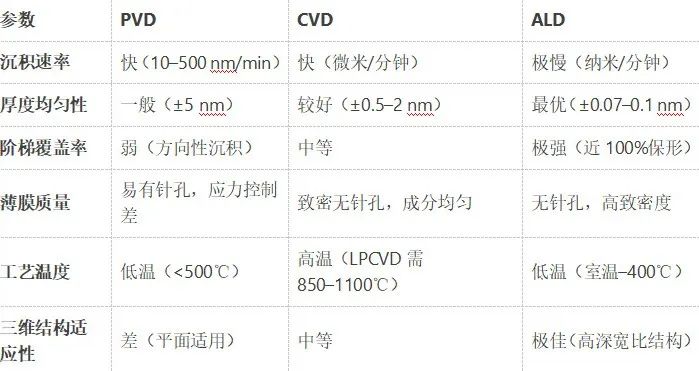
3. 核心应用场景
PVD:
金属薄膜:电极(
局限性:不适合深槽或高深宽比结构(如
3D NAND)。CVD
:介质与半导体薄膜:SiO₂绝缘层、Si₃N₄钝化层、多晶硅栅极、钨插塞。
主流工艺:占薄膜沉积设备市场的
57%(PECVD占33%)。ALD:
先进制程关键应用:
High-k栅介质(HfO₂、Al₂O₃,用于28nm以下逻辑芯片)。
3D NAND字线填充(深宽比50:1以上)。
FinFET/GAA晶体管中的间隔层(Spacer)。
特殊需求领域:生物相容涂层、催化材料、纳米器件。
4. 技术优势与挑战
PVD:
优势:设备简单、沉积快、成本低。
挑战:台阶覆盖率差,薄膜均匀性难控。
CVD:
优势:成分精确、覆盖性好,适用材料广泛。
挑战:高温易损器件,副产物可能污染薄膜。
ALD:
优势:原子级精度、无针孔、低温工艺。
挑战:沉积速率慢,设备成本高,量产效率依赖循环优化(微导纳米达
15,000片/小时)。5. 市场趋势与国产化进展
市场份额:
CVD占主导(57%),ALD占比11%但增速最快(2020–2025年CAGR=26.3%)。
国产化现状:
PVD设备:国产化率约20%(北方华创主导)。
CVD/ALD设备:国产化率低,但拓荆科技(PECVD)、微导纳米(ALD)已突破28nm High-k工艺。
驱动因素:
先进制程(3nm需超100道薄膜工序)要求更高精度。
3D器件结构(如FinFET、GAA)依赖ALD的三维保形性。
总结:技术定位与发展方向
PVD:金属薄膜沉积的经济方案,适合平面结构。
CVD:通用型主流技术,覆盖多数介质/半导体薄膜。
ALD:先进制程的“精密工具”,不可替代性随器件微缩增强。
未来趋势:
ALD将加速渗透逻辑/存储芯片制造,而CVD仍主导中厚膜沉积;国产设备在ALD领域亟待突破高精度反应腔室与前驱体输送系统。*主要参考来源:
薄膜沉积设备技术可分为PVD、CVD和和ALD工艺,工艺原理各有不同
https://www.leadingir.com/hotspot/view/3845.html
半导体技术中的薄膜沉积
https://www.chem17.com/tech_news/detail/1872636.html
相关阅读
芯启未来,智创生态





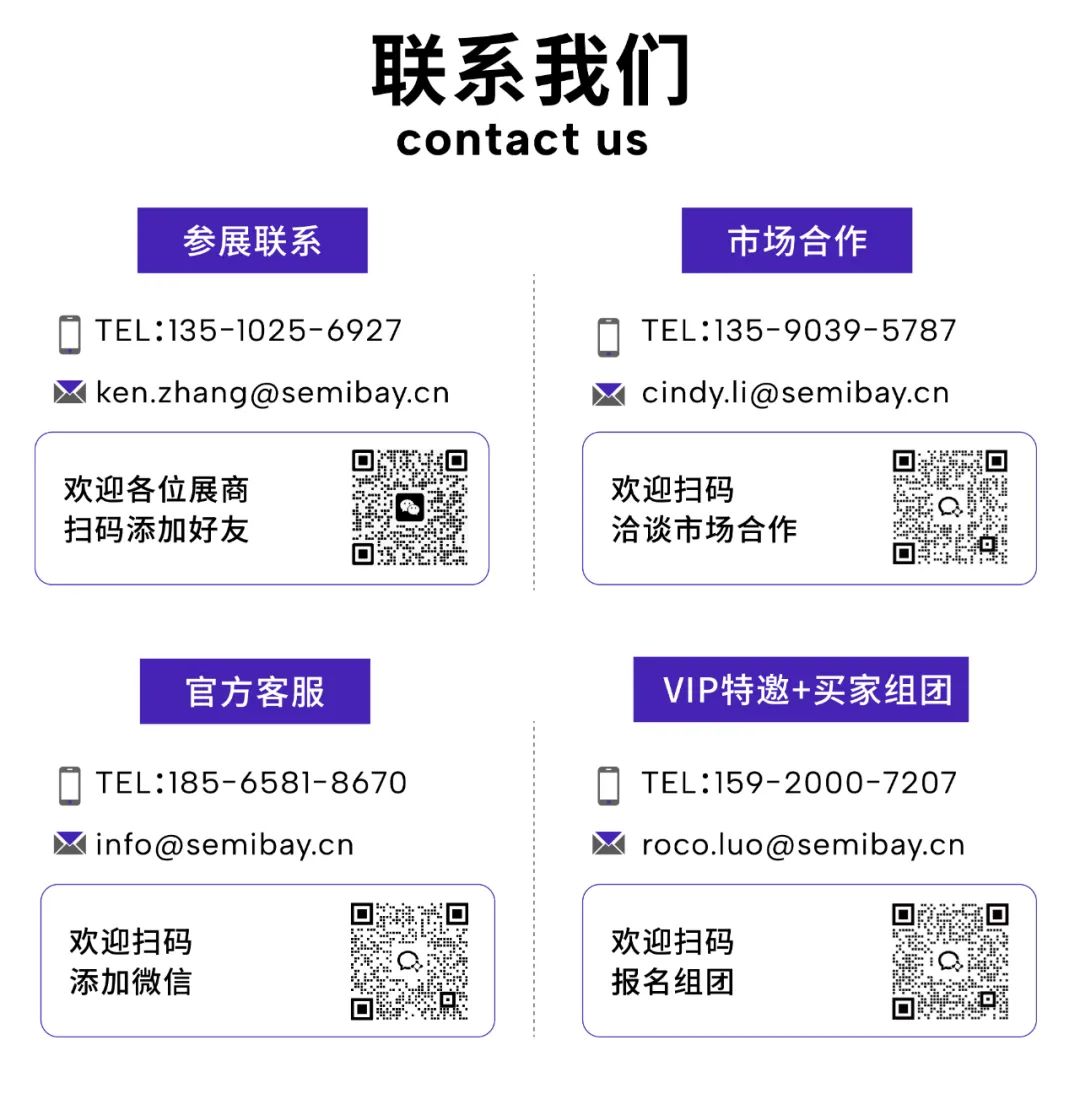
