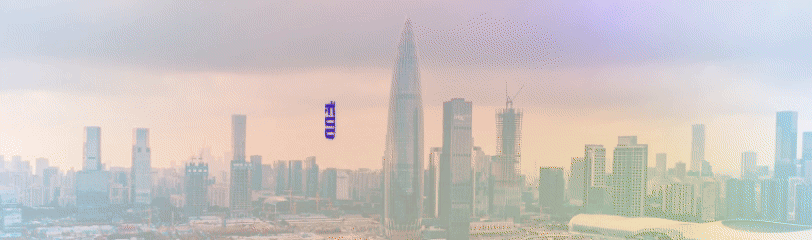
【编者按】
我们向万能的DeepSeek提出一些简单的半导体相关问题,看其回答能否满足你的要求。
问题:湿法清洗和干法清洗两种清洗技术的对比分析
半导体制造中的清洗工艺至关重要,它直接影响器件的良率和性能。湿法清洗和干法清洗是两种核心技术,各有优势和局限。以下是对它们的详细对比分析:
一、基本原理与机制
湿法清洗:
原理: 利用化学溶液(酸、碱、氧化剂、溶剂、表面活性剂等)的溶解、氧化还原、络合、润湿等化学作用,结合超声波、兆声波、喷淋、旋转等物理作用,去除晶圆表面的污染物(颗粒、有机物、金属杂质、自然氧化层等)。
机制: 化学反应为主,物理辅助(增强质量传递和去除力)。需要在液体环境中进行。
干法清洗:
原理: 在气相或等离子体状态下,利用活性气体(通常是等离子体活化产生的自由基、离子、激发态分子)与晶圆表面污染物发生化学反应(挥发化)或物理轰击(溅射)来去除污染物。
机制: 物理轰击和化学反应相结合(等离子体清洗为主),或纯化学反应(气相清洗如HF气相刻蚀)。在真空或低压气体环境中进行。
二、主要优缺点对比




三、关键对比维度总结
污染类型针对性:
湿法: 强于颗粒、有机物、部分离子。
干法: 强于金属污染物(尤其是难去除的)、精确去除薄层、选择性去除特定材料。
工艺控制与损伤:
湿法: 控制相对简单,但干燥环节易出问题;化学腐蚀需精确控制。
干法: 控制参数多且复杂;等离子体物理轰击易造成表面/界面损伤和电荷积累(对先进节点栅氧威胁大)。
材料兼容性与结构适应性:
湿法: 液体能渗透复杂结构,均匀性好;但对某些材料(如多孔低k介质)浸润可能有问题。
干法: 在高深宽比结构中可能不均匀(微负载效应);对敏感材料(如超薄栅、某些金属)的等离子体损伤风险高。
成本:
湿法: 设备初始成本低,但运行成本(化学品、水、废液处理)高。
干法: 设备初始投资高,但运行成本(化学品消耗少)相对较低。
吞吐量:
湿法: 批处理(多片同时处理)通常吞吐量更高。
干法: 单片处理为主,吞吐量相对较低(但集成在Cluster Tool中可提高整体效率)。
环保性:
湿法: 废液处理压力大,环保成本高。
干法: 更环保,化学品消耗和废物产生少。
四、发展趋势
干法清洗比重增加: 随着工艺节点不断缩小(特别是进入纳米节点后),对金属污染控制、无损伤清洗、无液体工艺的需求剧增,干法清洗在FEOL(特别是栅极形成前)的应用越来越关键和广泛。
湿法持续优化: 湿法在颗粒去除、有机物去除、批处理效率方面仍有不可替代性。发展方向包括:更低化学品浓度、更低表面张力溶液(减少图案倒塌)、更高效的干燥技术(如马兰戈尼效应干燥、异丙醇蒸汽干燥)、单晶圆湿法设备(提高工艺控制、减少交叉污染、便于集成)。
混合清洗技术: 结合湿法和干法的优势,在一个工艺模块或流程中先后使用两种技术,以达到最佳清洗效果(例如,干法去除金属后湿法去除颗粒和有机物)。
新型干法技术: 如超临界CO2清洗、低温气溶胶清洗等,旨在减少等离子体损伤的同时保持干法的优势。
面向新材料与新结构: 针对GAA晶体管、3D NAND、高深宽比DRAM等新型结构和新型材料(如2D材料、新型金属栅/高k介质),开发更温和、选择性更好、损伤更小的清洗技术(干法和湿法均在持续创新)。
结论
没有绝对优劣,只有最适合特定应用场景的技术。现代半导体制造线中,湿法清洗和干法清洗是互补共存、相辅相成的关系。
湿法清洗在去除颗粒、有机物、批处理效率方面有优势,是成熟且不可或缺的基础工艺,尤其在BEOL和某些对金属污染要求相对宽松的环节。但其废液处理成本和干燥挑战是痛点。
干法清洗在去除金属污染物、精确控制、无液体处理、工艺集成和环保方面优势明显,已成为先进制程(尤其是FEOL核心步骤)的关键技术。其设备成本和潜在的等离子体损伤是需要关注和解决的问题。
发展趋势是干法清洗在关键步骤的应用日益增多,湿法清洗持续优化并向单晶圆和更环保方向发展,同时混合清洗技术也受到重视。选择哪种技术取决于具体的污染物类型、工艺步骤要求(如对金属污染的容忍度)、器件结构、成本效益和环保法规等多方面因素。
相关阅读
芯启未来,智创生态





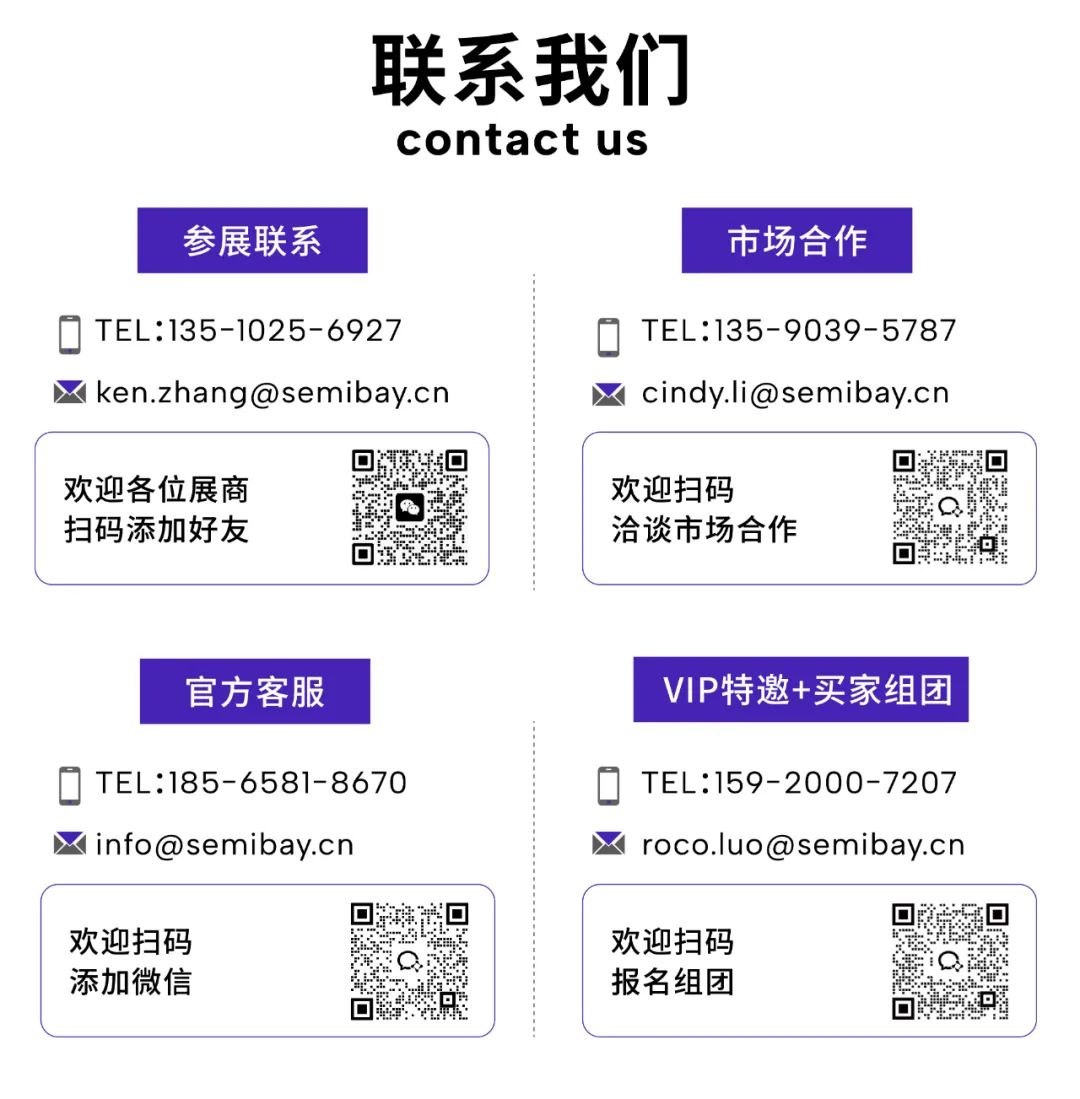
