摘要:在传统的金属钣金类加工场景中,使用模具裁切落料是比较广泛的加工方式,但因模具设计存在制造周期长、成本高等问题,故仅适用于大批量或高附加值产品等有限的场景中;对于小批量及复杂工件加工的场景,拥有较高加工精度及柔性化的工业机器人激光切割应用已逐步成为最佳解决方案。由于传统的工业机器人手工示教编程耗时长、精度偏低,因此工业机器人离线编程技术得到越来越多用户的青睐。然而,工业机器人离线编程技术自身也存在诸多制约性因素:如无法脱离产品3D模型图、离线编程轨迹程序导入工业机器人本体后仍需要对刀校准,以及在实际工件上完成的切割效果也会因整体布局的综合精度影响而表现不一,因此离线编程技术至今尚未能全面替代传统的手工示教编程。将结合个人经验与案例,阐述工业机器人离线编程在激光切割应用中的使用优势,涉及的难点与关键因素,以及行业应用现状。
关键词:工业机器人切割;工业机器人离线编程;激光切割;工业机器人应用
作者:川崎机器人(天津)有限公司 杨晟
1 序言
激光技术于20世纪60~70年代开始应用[1],在工业领域中尤以焊接及切割为主。传统激光切割设备主要分为平板激光切割机、管材型材类激光切割机、三维多轴激光切割机与机器人激光切割单元4类。机器人激光切割方式普遍是直接将激光切割头安装在六自由度工业机器人(以下简称“机器人”)JT6轴法兰盘上,通过机器人运动姿态的变化,实现工件外围轮廓和定位孔切割[2]。机器人切割单元因具有多样化功能及优异的柔性加工特性等优势而被广泛用于诸多领域。行业内比较常见的机器人离线编程软件如VC、Robotguid、RobotStudio、K-Roset及Delmia等,均为各机器人厂商自主开发或第三方软件,主要用于数字孪生及虚拟仿真功能的实现与项目前期模拟评估。针对机器人激光切割离线编程且具有CAM功能的软件则很少,比较成熟的软件有来自加拿大的Robmaster、俄罗斯的SprutCAM及日本的KCONG等。前两者为第三方软件厂商,支持或可扩展各品牌机器人的模型数据导入与离线编程,其中SprutCAM因性价比高、软件功能强大等优势,在我国工业领域占比较高;KCONG为日本川崎机器人厂商自主开发软件,仅支持川崎机器人的离线编程,虽然不能同其他第三方软件一样支持各品牌机器人模型数据,但其与机器人自身功能结合效果最佳,在机器人实机调试上表现效果也更为出色。
2 离线编程优势
在机器人切割应用中,很多场景还是在使用传统的手工示教编程(即在线编程),在线编程是在实时环境下进行的编程,操作人员将机器人与计算机实时连接后进行现场调试[3];机器人离线编程(Off-Line Programming,OLP)系统是机器人编程语言的拓展,它利用计算机图形学的成果,建立起机器人及其工作环境的模型,再利用一些规划算法,通过对图形的控制和操作,在不使用实际机器人的情况下进行轨迹规划,进而产生机器人程序。离线编程具备较优的界面美观性与友好性,可加快编程效率[4,5],对比手工示教编程,离线编程系统还有如下优势。
1)编程调试占用机器人设备时间短,大幅提高了生产设备的稼动率,间接性帮助了产能的提升。
2)可在软件的虚拟环境中完成机器人轨迹执行的验证。预见可能发生的机器人动作报警或碰撞干涉,从而减少了设备实机上出现的问题甚至撞机损坏。
3)即使在没有实际产品参照的情况下,也能够根据3D模型编制出轨迹程序,引导机器人切割出最终需要的产品轮廓,这是手工示教根本无法做到的。
4)还可根据工件结构特性、加工工艺要求、路径特征等参数类型,建立起标准化数据库,在相似的场景下重复调用,进一步提高了编程调试效率。
3 离线编程的工作流程
离线编程必不可少的要素就是使用计算机3D模型数据,将包含机器人本体、周边设备、加工工具及工件等图形元素在内,构建出一个虚拟的机器人作业场景,如图1所示。
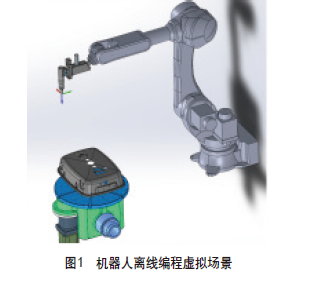
从3D模型数据的处理开始,到机器人实机执行动作路径共需5个环节,即:3D模型转换→制作生成路径→示教点(轨迹)生成→模拟演示确认→程序导出至机器人及实机调整。
4 离线轨迹生成后的实机调试
(1)工具坐标TCP登录 工具坐标TCP,即机器人识别自身工具上的参考点坐标,通常使用4~6点法登录此值。在激光枪前端安装标准的顶针,针尖即激光的焦点,同时也是机器人的工具坐标系TCP;另外,在机器人旁边再固定一个顶针,也称为测量规尺,示教操作机器人依次以多个不同的姿态使2个顶针针尖对齐,如图2所示。同时,将多个姿态下的坐标参数登录到机器人系统内,创建出工具坐标系,即TCP。
(2)外部轴参数登录 有些场景中机器人还会安装外部轴,如承载机器人本体移动的导轨或承载工件转动的变位机,以此来增加机器人运动的自由度及动作范围,如图3所示。由于外部轴机构与机器人手臂本体不是一体化结构,故需要在机器人系统内将外部轴与机器人本体的位置关系参数进行计算及登录,通常使用机器人专用程序或在机器人系统功能菜单内进行两者位置关系的校准计算。但外部轴设备会增大离线编程输出轨迹数据的偏差,无法对应激光切割领域中加工精度要求较高的场合,因而在弧焊领域应用更为广泛。
(3)工件坐标系登录 在机器人行业,也称作用户坐标系或框架坐标系等。各厂家定义名称不同,但使用原理基本相当,均是在工件上或工件定位平台上创建出的参考坐标系,类似于数控机床的G54~G59加工坐标系。通过3~4个参考点将多段轨迹约束在一个三维空间坐标系上,无论是从离线软件到机器人,或是不同机器人之间的轨迹复制,均可通过这几个参考点将坐标系重新校准,从而达到轨迹随之准确迁移的目的,如图4所示。
(4)轨迹动作确认 在全部参数计算及登录完毕后,采用手动及低速自动模式执行离线编程导出的轨迹数据,以确认机器人运动过程中是否存在干涉、运动报警或轨迹偏差等问题。
(5)轨迹精确修正 即使以很高的精度完成了校准过程,还会在不可避免的人为操作误差、工件自身尺寸误差等因素的综合影响下,使最终执行轨迹存在0.1mm至几毫米的偏差,均属正常范围。此时就需要对完成的轨迹进一步精确修正,直至达到理想状态。
5 离线编程在激光切割应用中的难点
(1)机器人工具坐标系TCP精度 也称工具坐标系精度,即机器人设定的激光切割枪的激光焦点相对于机器人6轴法兰盘中心的位置精确度。此精度至关重要,会影响机器人动作姿态变化时激光焦点按预定轨迹行进的准确性及工件位置的校准精度,是整个离线编程切割精度的核心环节。
影响TCP精度的因素至少包括3点:①机器人手臂机械结构精度,如六关节机械手的各关节J1~J6,从机械手固定底座开始向加工头依次排开,显而易见这6个轴(关节)相互均不独立,因此精度误差会累积产生[6]。②机器人各轴零点绝对精度。③工具坐标系TCP登录时的操作精度。在外资品牌机器人厂商范围内,此精度会根据设备出厂时的状态,通常能达到0.1~0.5mm。
(2)工件坐标校准精度 即使在较高的工具坐标系TCP精度前提下,离线轨迹还需要在实际工件上进行工件坐标系的校准操作。目前,主要是由人工目测校准或传感器辅助测量计算两类方式完成。第一种方式需要事先准备辅助工装治具配合实施校准,在保证加工精度以及精细的人工目测下能够大幅减小综合误差,最终产生的误差通常会小于第二种方式,但需要操作人员在机器人上进行一系列手动示教操作,自动化程度较低。第二种方式会受到传感器与机器人间的标定精度、传感器自身的测量精度影响,虽然综合误差普遍大于第一种方式,但此方式可实现完全免示教执行工件坐标系的校准,自动化程度相对更高。
(3)机器人手臂运动过程的稳定性 此情况多发生在机器人运动过程中,当触及机器人某些特定的运动区域内(一般为机器人动作范围的最近或最远的极限区域附近)时,机器人手臂在运动过程中因加减速的变化而发生微小的颤动,即使人为目测没有发现,但通过仔细观察产品完成切割的轮廓,还是能观察到微小的波浪纹,对于品质要求很高的产品就无法满足。因此,部分用户会为机器人增配变位机或走行轴等外部轴装置,以扩大机器人的运动范围,使各段轨迹能够避开机器人的极限动作区域。
(4)工件产品尺寸误差 任何工件产品相对于理论3D模型或工件相互之间的尺寸均存在公差,尺寸越大、结构越复杂的产品公差范围也越大,工件之间一致性也就越差,此偏差无法通过离线编程软件直接解决,也是目前行业内最大的难点。
在上述多个环节累积偏差影响下,最终离线编程输出的轨迹数据很难完成超高精度要求的切割加工,严重的会直接导致产品不合格甚至报废,从而限制了离线编程技术的应用场景。因此,当下激光切割离线编程技术在多数场景仍然无法完全摆脱轨迹导入机器人本体后需要继续精确修正的局面。
另外,还可以通过机器人轨迹程序数据+相应算法相结合的方式进行补偿,需补偿的数值可以通过手工测量或传感器检测等手段获得,并将补偿数据代入到轨迹程序中。只是不同形状的工件,以及同一工件上不同部位的尺寸偏差也各有不同,轨迹补偿的算法也很难统一化,可能需要花费大量的时间对离线编程软件功能及其轨迹程序算法进行功能开发,在当前国内市场环境下,因大多产品都具有小批量、品种替代较为频繁、不同品种的产品之间差异化较大,很难共用相同的算法补偿,导致前期对离线编程软件及轨迹算法补偿功能的开发成本居高不下,所以轨迹自动补偿功能目前仅停留在极少的应用场合中,无法广泛普及。
6 离线编程在激光切割实际案例中的表现
某钢管激光切割案例中, 钢管外径2 5 . 4 ~50.8mm,壁厚1.0~1.2mm,产品规格总计4种。需要在钢管上切割一条闭合的相贯线,如图5所示。切割后与其他钢管装配供下道工序焊接,要求装配缝隙<0.5mm。此案例起初使用手工示教编程,切割完成的轮廓无法保证平滑性,轮廓偏差最大将近1mm,如图6所示。使用离线编程技术后,在精度及调试作业效率都展现出了明显的优势(见图7、表1),特别是在实机调试所占用设备的工时上,可大幅提高设备的生产稼动率达300%以上。
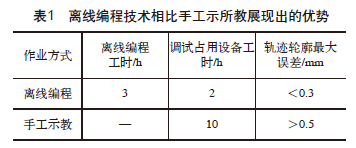

7 结束语
通过对机器人激光切割离线编程技术在实践过程中面临的问题点进行阐述,为诸多计划使用机器人离线编程技术的用户明确了应用概念及技术水平现状,对工程项目可能发生的潜在风险作出预警;同时,对机器人制造厂家及离线编程软件厂商,也具有一定的参考意义。随着智能制造的不断升级,机器人本体制造及校准精度持续提高,运动控制算法不断改进,未来再配合持续优化升级的各类传感器辅助校准,一定能够将离线编程技术的优势发挥到激光切割实践中,使机器人离线编程技术得到行业内的普遍认可及更加广泛的应用。
参考文献:
[1] 陈俐,巩水利,何恩光. 激光去除与连接技术发展研究[J]. 中国工程科学,2020(3):86-92.
[2] 孙加强,焦俊科,张文武,等. 基于ABB机器人的光纤激光切割与焊接系统研究[J]. 应用激光,2014,34(6):584-588.
[3] 马少龙,梁舒,陈明辉. 基于离线编程技术的工业机器人绘图系统研究[J]. 现代制造技术与装备,2020,56(7):65-66.
[4] 解海亮,黄思,王天正,等. 双机器人紧协调焊接路径规划与离线编程[J]. 机械设计,2022,39(8):96-103.
[5] 程晓飞,高胜,李军,等. 马鞍形焊缝焊接机机器人设计与建模分析[J]. 焊接学报,2022,43(3):95-100,126-127.
[6] 郭澄若,村井融. 三维激光切割加工中若干问题探讨[J]. 金属加工(冷加工),2016(21):39-40.
☞来源:《金属加工(热加工)》2025年第6期☞责任编辑:游小秀☞审核人:张维官
☞广告合作: 孙哿 13811718902